FORM 5S1408
AIR COMPRESSORS
2433
2570
5815
Installation (continued)
COMPRESSOR HEAD (AIR PUMP)
Make certain that the compressor head is fastened securely to
the mounting saddle or deck.
NOTE: The flywheel should be assembled to the unit with
the set screw (or fastening bolt) and the arrow on the
outside of the crankshaft. Tighten set screw on the key.
BELTS
Drive belts must be kept tight enough to prevent slipping. If
belts slip or squeak, the motor should be adjusted for proper
tension. If belts are too tight, overload will be put on motor and
compressor bearings. Belt tension is correct when normal
thumb pressure depresses belt 1/4 to 1/2". Pulleys should be
properly and carefully aligned.
IMPORTANT: Whenever possible, belt guards should be used!
ELECTRICAL
Have all electrical connections made by a competent
electrician.
All wiring and electrical connections must comply with the
National Electrical Code, and local electrical codes in effect. In
particular, refer to Article 430 (Motors, Motor Circuits and
Controllers) of the NEC.
For Proper motor connections, refer to the connection diagram
located on the nameplate or inside the terminal box. Make
sure connections are correct for the voltage being supplied the
motor.
Motor should be grounded by use of a separate grounding
conductor, connected to the motor frame. Verify that the
ground wire runs to a good electrical ground such as a
grounded conduit or water system Insure that a good ground is
provided at the supply end of the line. Connections should be
made with flexible conduit to minimize vibration transmission.
Avoid use of extension cords on portable units. If an extension
cord must be used, keep length as short as possible. Use
heaviest wire size cord available, and do not use less than size
and gauge indicated, below.
WIRE SIZE CHART
MINIMUM WIRE SIZES FOR EXTENSION CORDS AND
PERMANENT WIRING
25 Ft.
50 Ft.
100 Ft.
HP
115V
230V
115V
230V
115V
230V
1/2
14
16*
12
16*
8
14
3/4
12
16*
10
16*
8
14
1
12
16*
10
14
6
12
1 1/2
10
14
8
14
6
12
2
10
14
6
12
4
10
* Use only #14 AWG or larger wire for permanent installations.
Operation
The crankcase of this compressor was drained before shipping.
Before operating compressor, with a good grade of unused, clean
oil. See chart below.
RECOMMENDED COMPRESSOR OILS
1. American Oil Company:
A.
Amoco Industrial Oil
No. 53
B.
Amokon No. 35
2. Texaco, Inc. - Texas Regal C-R&O
3. Exxon Company:
A.
Teresstic 52
B.
Esstic 50
C.
Nuto 53
4. Fiske Brothers Refining Co. -
Lubriplate
Non-Detergent
Motor
Oil SAE 20
5. Clark Oil & Chemical Co. - Co Chem #228
6. Phillips Petroleum Co. - Baltic Grade 315
7. Gulf Oil Corp. - Gulf Harmony Oil C
8. Continental Oil Co. - Conoco Dectol Medium
Except for Fiske, these are all non-detergent, rust and oxidation
inhibited industrial oils with the viscosity equivalent to a SAE
Grade 20 weight motor oil. These oils will work satisfactorily for
temperature ranges between 20° and 90o F. This should take care
of most installations. For applications where the ambient
temperature is consistently above 90° F., the next higher viscosity
oil in these same oil families should be used.
NOTE: DURING BREAK IN, CAREFUL AND REGULAR CHECK
OF OIL LEVEL SHOULD BE EXERCISED. MAINTAIN OIL AT
FULL LEVEL. REFER TO THE MAINTENANCE SECTION FOR
ADDITIONAL LUBRICATION INFORMATION.
Fill engine crankcase (if gasoline engine operated in accordance
with engine manufacturers recommendations found in engine
manual.
WARNING: NEVER ADD GASOLINE TO A HOT ENGINE!
IMPORTANT: Before proceeding with work operations, make
certain that you are thoroughly familiarized with the function and
operation of each component in your system. READ ALL
INSTRUCTION MANUALS PERTINENT TO YOUR PARTICULAR
SYSTEM!
- 5 -
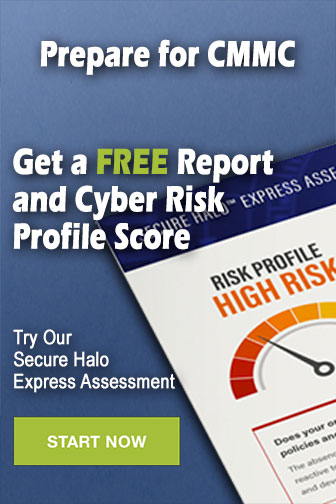