FORM 5S1408
AIR COMPRESSORS
2433
2570
Installation
5815
These air compressors are built to rigid specifications for long,
trouble-free life. Both A.S.M.E. code and non-code tank models
are engineered to perform all air compressing jobs within their
stated ratings and capacities. A correct Installation (Figures 2 &
3) is made when the following conditions are met:
LOCATION
Portable air compressors can be located, anywhere; however, if
possible, select a clean, cool, dry place. Permanently installed
compressors MUST BE located in a clean, well ventilated .room.
Compressors should never be located so close to a wall or other
obstruction that flow of air through the fan bladed flywheel, which
cools the compressor, is impeded. Permanently mounted units
should have flywheel at least 12" from wall. Rotation must be in
the direction such that pump flywheel fan, where used, blows air
toward the cylinder.
Place portable or stationary compressors on firm level ground or
flooring. Permanent installations seldom require bolting to floor;
however, bolt holes in tank or base feet are provided. Before
bolting or lagging down, shim compressor level.
IMPORTANT: Avoid putting a stress on a tank foot by pulling it
down to floor. This will only result in abnormal vibration.
DISCHARGE PIPING
The compressed air distribution system should be constructed of
pipe large enough so that the pressure drop between the air
receiver (tank) and the point of use will not exceed 10% of the
initial receiver pressure. Fittings offering least resistance to flow,
such as long radius elbows, should be selected. Provision
should be made not only for present requirements, but for
reasonable future growth as well. Refer to page 8, PIPING
REQUIREMENTS FOR AIR DISTRIBUTION SYSTEMS, for
additional information.
All main line piping should be sloped away from the compressor
at approximately 1/4" per foot to a drop leg at the lowest part of
the system. This makes it possible to drain the overnight
accumulation of moisture from the lines and prevent moisture
from draining back into the receiver. Outlets from the main line
should be taken from the top of the main by using a tee and two
elbows to get the necessary "U-shaped" connection as illustrated
in Figure 2.
NOTE: Do not place a shut-off valve in the discharge line
between the compressor head and the air receiver. However, he
use of a check valve to prevent back pressure damage to the
compressor head is essential.
AIR INTAKE
A clean, cool, dry air supply is essential to satisfactory operation.
The standard air filter supplied with the compressor is of
sufficient size and design to meet normal filtering requirements if
properly serviced. Paper-type filter elements SHOULD NOT BE
washed in solvent: instead, they should be blown out with
compressed air and replaced periodically. Foam-type filter
elements should be washed periodically with a household
detergent and blown dry. DO NOT OIL! Felt-pad filters should
be periodically blown out with an air jet. Replace filters if filled
with dirt or paint. Do not wash out or oil. If the compressor is to
be
installed
where
considerable
dust,
dirt
and
other
contaminants are prevalent, it is suggested that an oil bath filter
be substituted for the standard filter. (If this filter is used, be sure
to replace oil when dirty.)
If long runs of Intake pipe are necessary to supply the
compressor with cool air, the intake should be Increased by one
pipe size for each eight feet of added length beyond the intake
port of the compressor head. If the intake is piped to the outside,
a hood should be Installed over the filter to prevent the entrance
of rain and snow into the air intake.
RELIEF VALVE
The relief valve (safety valve) vents the tank if excess pressure
builds up. It has been adjusted for maximum pressure allowable
according to tank specifications and the working pressure of the
unit on which it is installed.
CAUTION: Do not readjust or modify for any reason!
CHECK VALVE
This is an automatic valve placed in the line between pump and
tank to prevent reverse pressure being applied to the valves of
the pump. Failure of valve will cause difficulty in starting the unit.
Often, noise problems and pump valve failures are caused by a
faulty check valve. On some models, a combination relief/unload
valve is used. Where such a valve is used, proper operation is
indicated by a brief spurt of air, when the pump stops, from the
small vent hole in the side. Continuous air flow, or no air flow at
all, indicates a defective valve.
TANK DRAIN VALVE
The drain is located at the bottom of the tank, which should be
drained at least once weekly. A strainer installed ahead of the
valve will help prevent solid particles such as carbon, rust or pipe
scale from fouling the tank drain valve.
PRESSURE SWITCH CONTROL
On pressure switch-controlled models, the pressure switch is
automatic and will start the compressor at the low pressure, stop
it when maximum pressure is reached.
PRESSURE SWITCH ADJUSTMENT:
WORKING RANGE (Large Spring) - Switches are set at the
factory to operate at the pressure indicated on the nameplate.
To raise operating pressure, turn the range spring nut down,
which compresses the range spring. Loosen the range spring
nut to lower the operating pressure.
DIFFERENTIAL (Small Spring) - Pounds pressure between
"Open", and "Close" is referred to as the differential. To increase
the differential, turn down the differential spring. By loosening
this nut, differential will be narrowed. (Differential adjustments
affect cut-out point only).
IMPORTANT: If the operating pressure is to be adjusted, the
following guide-lines MUST BE observed:
SINGLE STAGE UNITS - 100 psi maximum continuous running
pressure. Maximum intermittent duty pressure is 125 psi.
TWO STAGE UNITS - Maximum continuous running pressure
and intermittent duty pressure is 175 psi.
CAUTION: Keep hands away from moving parts, as the unit
may start unexpectedly.
- 4 -
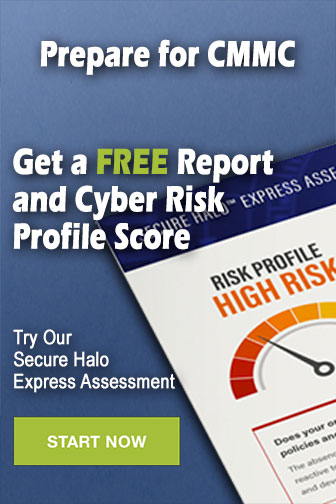