FORM 5S1408
AIR COMPRESSORS
2433
2570
Trouble Shooting Chart
5815
SYMPTOM
POSSIBLE CAUSE(S)
CORRECTIVE ACTION
Low discharge
1.
Air leaks.
1.
Listen for escaping air. Apply soap solution to all fittings and
pressure.
connections. Bubbles will appear at points of leakage. Tighten
or replace leaking fittings or connections.
2.
Leaking valves.
2.
Remove valve assemblies or-plates from the head, disassemble
and inspect for valve breakage, weak valve springs or plates,
scored valve seats, etc. Replace defective parts and reassemble.
CAUTION: Be sure that old valve assembly or head gaskets are
removed and are replaced with new ones each time the valve
assemblies are removed from the head.
3.
Restricted air intake.
3.
Clean the air filter element. Check for unnecessary elbows in
the intake line, and remove if they are materially restricting the
flow of intake air to the compressor.
4.
Slipping belts.
4.
Loosen motor clamping bolts and move the motor in a direction
away from the compressor, being sure that the motor shaft is
perfectly parallel to the scribed line. Tighten motor clamping
bolts. Normal thumb pressure should deflect belts 1/4 to 1/2.
Do not "roll" belts over pulleys.
5.
Blown Gaskets.
5.
Replace any gaskets proven faulty on inspection.
6.
Low compression.
6.
Low pressure can be due to worn rings and cylinder walls.
Correction is made by replacing the rings, cylinders, and pistons
as required.
Over-heating
1.
Poor ventilation.
1.
Relocate the compressor to an area where an ample supply; of
cool, clean, dry and well circulated air Is available.
CAUTION: Avoid locations near boilers or other areas where
there is a high ambient temperature
2.
Dirty cooling surfaces.
2.
Clean the cooling surfaces of the cylinder, intercooler and
aftercooler.
3.
Incorrect pulley rotation.
3.
Check the arrow on the pulley for correct rotation. If incorrect,
have a competent electrician reverse the motor rotation. Air flow
should always be toward the cylinders (on units with fan-type
flywheel).
Unit stalls
1.
Overloaded motor
1.
Have competent electrician examine the motor and wiring, then
proceed with his recommendations. Check motor voltage
connection.
2.
Low or unbalanced
2.
Same as No. 1 above.
voltage.
3.
Improper lubrication.
3.
See lubrication section on following page.
4.
Excessively long or
4.
Avoid use of extension cords wherever possible. If extension cord
undersized extension
used, minimize length. Use largest size cable available.
cord.
Excessive belt
1.
Pulley out of alignment.
1.
Realign motor pulley with compressor pulley.
wear
2.
Belt too loose or too
2.
Adjust tension.
tight.
3.
Belt slipping.
3.
Adjust tension
4.
Pulley wobble
4.
Check for worn crankshaft, keyway or pulley bore resulting from
running the compressor or motor with loose pulleys. Check for
bent pulleys or bent crankshaft.
- 6 -
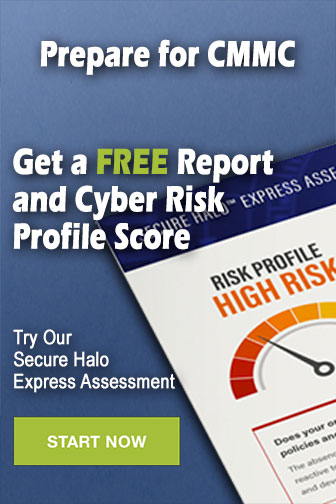