TM 9-4940-342-14&P
dome drain valve. (refer to fig 2-1, item 31 and 38.)
3-10. To check oil level in water pump, remove oil
fill plug. If oil level is below oil fill plug opening,
add SAE 20 non-detergent oil.
3-11. To check fuel oil filter, close fuel valve,
remove element, and clean out any accumulated
sediment and water. Replace element and secure.
(refer to fig 2-1, item 39.)
3-12. To blow down unit proceed as follows (refer
to fig 2-1).
a. Blow down unit after each day's use or every 8
hours of operation as follows:
(1) Stop the cleaner as described in operation
procedures.
(2) Remove steam hoses from both discharge
outlets and close discharge valves (32).
(3) Place selector valve (8) in open (horizontal)
position and open air dome drain valve (31).
(4) Turn on pump control switch (4) and burner
switch low (1).
(5) Depress and hold blow-down switch (37).
After a purge delay, the low fire burner will ignite.
Hold blow-down switch and allow burner to operate
for approximately 30 seconds.
(6) Release blow-down switch (37) and shut off
burner switch low (1) and pump control switch (4).
(7) Steam and residue should discharge from
the air dome drain valve. When the flow of steam
and residue has stopped, close the air dome drain
valve (31).
(8) Place selector valve (8) in closed (vertical)
position.
(9) Open discharge valves (32) and turn on
pump control switch (4). Dry steam and residue
should discharge from both discharge valve hose
outlets.
WARNING
Do not stand, or allow other personnel to stand, in
front of discharge valve outlets during preceding
procedure and avoid contact with hot water and/or
steam from outlets.
(10) When all steam and residue are flushed out
of discharge valve outlets and water is cool, shut off
pump control switch (4).
(11) Reconnect steam hose to discharge valve
outlets. The cleaner is now ready for normal
operation.
NOTE
If coil outlet temperature on gage (10) exceeds 370°F
in step 10, the over temperature switch (26) will have
to be reset before the cleaner can be fired.
NOTE
If repeated blow-down operations fail to reduce scale
buildup (excessive back pressure), an acid washing of
coils shall be accomplished.
3-13. When repair of light assembly is required,
remove the light bulb and replace (refer to fig 2-1).
3-14. The oil cap assembly is replaced when
inspection determines the need for repairs (refer to
fig 2-1).
16
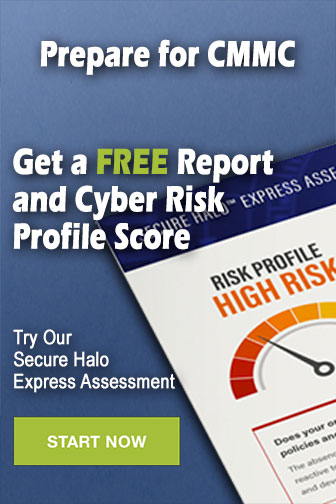