TM 9-4940-342-14&P
CHAPTER 3
OPERATOR'S MAINTENANCE INSTRUCTIONS
Section I. PREVENTIVE MAINTENANCE CHECKS AND SERVICES (PMCS)
3-1. Lubrication Instructions
There are no lubrication requirements for the oil
fired steam cleaner model 6000-OM.
3-2. General
To insure that the steam cleaner is ready for
operation at all times, it must be inspected
systematically, so that defects may be discovered and
corrected before they result in serious damage or
failure. The necessary preventive maintenance
services to be performed are listed and described in
paragraphs 3-3 and 3-4. The item numbers indicate
the sequence of inspection requirements. Defects
discovered during operation of the equipment shall
be noted for future correction, to be made as soon as
operation has ceased.
Operation shall be stopped immediately if a
deficiency is noted which would damage the
equipment if the operation were continued. All
deficiencies and shortcomings will be recorded,
together with the corrective action taken, on DA
Form 2404 (Equipment Inspection and Maintenance
Worksheet) at the earliest possible opportunity.
3-3. Operator Preventive Maintenance Services
Table 3-1 contains a listing of preventive
maintenance services which must be performed by
the operator. The item numbers are listed
consecutively and indicate the sequence of minimum
requirements. Refer to table 3-1 for the preventive
maintenance services.
Table 3-1. Operational Preventive Maintenance Checks and Services
B - Before operation D - During operation A - After operation
Interval
and
Sequence No
Item to be inspected procedure
Work
Time
(M H)
B
D
A
NOTE
Visually inspect, concurrently with the daily checks and ser-
vices, for proper fuel oil and detergent levels and fuel leaks.
1
31
45
Drain air dome every four (4) hours during operation.
0.2
2
Check oil level in water pump.
0.1
3
Check fuel oil filter.
0.1
32
Blow down unit every eight (8) hours during continuous operation.
0.2
4
Check soap solution level.
0.1
5
Check fuel oil level.
0.1
6
33
Inspect hose assemblies for leaks and frays.
0.1
7
34
Inspect gun assemblies for clogged nozzles.
0.1
8
Inspect water tank assembly for leaks and signs of rust.
0.1
9
35
Inspect plumbing assembly for leaks and loose joints.
0.1
10
36
Inspect water pump assembly for leaks.
0.1
11
Inspect motor assembly for loose mounting and frayed wiring.
0.1
12
37
Inspect oil pump assembly for leaks and tightness of hardware.
0.1
13
38
Inspect coil inlet assembly for leaks.
0.1
14
Inspect burner plate assembly for burned ignitors and tightness of
0.3
hardware.
15
39
Inspect coil outlet assembly for leaks.
0.1
16
40
Inspect pressure gages for broken and cracked glass, check for leaks
0.1
and tightness of fittings.
17
Inspect hourmeter for legible numbers and broken glass.
0.1
18
Inspect light assembly for broken bulb.
0.1
19
Inspect toggle switches for tightness of hardware and loose con-
0.1
nections.
13
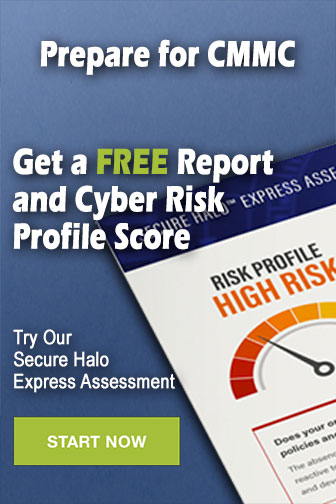