TM 10-4610-232-12
NOTE
This leaves the RO vessels full of the sodium bisulfite sanitizing solution. Drain only if the
ROWPU will be subject to freezing (para. 2-31).
(18)
Open system pressure control valve (15).
(19)
Return to the shutdown procedures, continue with instructions provided in para. 2-22b (9) for short term or para. 2-23f (2)
for long term.
2-27. OPERATION OF AUXILIARY EQUIPMENT. Auxiliary equipment deployed with the ROWPU includes:
a.
M871 Trailer. Refer to TM 9-2330-358-14&P.
b.
Diesel Generator. Refer to TM 5-6115-545-12 or TM 9-6115-645-10.
c.
Potable Water Storage Tanks. Refer to TM 5-5430-225-12&P.
WARNING
Do not exceed load limits of hoist. Do not operate hoist without safety latches on hooks.
Failure to observe these precautions could result in serious injury and damage to
equipment.
d.
Chain Hoist. The chain hoist is used for lifting the distribution pump and raw water pump out of, and into, the ROWPU during
unloading (para. 2-14) and packing the ROWPU (para. 2-28). It is also used to move large items for maintenance. The hoist
has a 1/2 ton capacity. It has safety latches on both the mounting hook and the load hook. Refer to para. 2-14c. Check
Preventive Maintenance, Table 2-13.
2-28. PREPARATION FOR MOVEMENT.
a.
Loading Procedures and Load Plans. The following instructions will describe in detail the proper procedure when loading a
3000 gph ROWPU, Models WTA-060 and ROWPU-1. The packing instructions for both models will be identical unless
otherwise indicated. This packing guideline is provided to ensure each ROWPU is packed correctly to avoid damaging
equipment while being transported. NCO's must understand the importance of proper loading procedures and that they will be
held accountable for damages caused by incorrect packing procedures.
(1)
The interior of the van should be cleaned each day during operations when filtered and potable water is most abundant
This will make cleaning easier at the close of an operation.
(2)
The floor of the van and any other equipment should be washed with either fresh filtered water or potable water only.
When purifying with saltwater, do not use filtered water to clean the interior of the van or any other equipment. Water
from the cartridge filter sample hose has not gone through the RO process and therefore is filtered saltwater not filtered
fresh water This will cause corrosion to the equipment.
(3)
Enough potable water should be available at the end of a mission for the purpose of distribution and field cleaning
equipment before packing. Equipment cleaning should begin 2 to 3 days prior to shutdown to allow the equipment to dry.
(4)
Before packing the van, ensure the ROWPU is as clean as possible and all end item components am clean and dry.
Equipment stored wet will mold, grow bacteria, and will have an unpleasant order. Equipment with such conditions cannot
be used for treatment purposes.
(5)
100% inventory by hand receipt must be conducted after each mission. Hand receipt holders must be watchful of items
being taken into the van to ensure they are properly marked on the hand receipt. Serial numbered items must be
accounted for when loading. All storage boxes must be inventoried before they are loaded. Any shortages will be noted
on DA Form 2062 and turned in. An investigation will be conducted on any sensitive or high dollar items listed as missing.
b.
System Support Items (Table 2-31). The support items are packed into four separate storage boxes. Dividers are provided for
box 1; heavy items in boxes 2, 3 and 4 should be on bottom to prevent damage to equipment.
Change 12 2-129
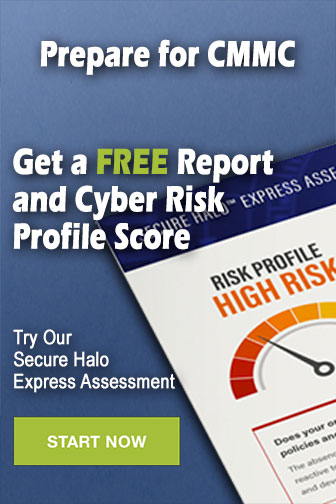