SETTING UP
Your 17" Variable Speed Drill Press was completely
assembled and tested at the factory. When selecting floor
space
please
note
that
vibration
transmitted
through
inadequately constructed floors by adjacent machinery or other
source can impair the accuracy of your machine. Supplied
with your drill are four anti-vibration pads and four steel plates.
When the drill is moved to it's permanent shop location,
position the four anti-vibration pads and the four 1/16" steel
plates under each corner of the drill press base, with the steel
plates between the pads and the base of the drill. If the
machine is to be fastened to the floor, the compressed height
to the top of the steel plates should be 5/16".
The head ad table of your drill press have been lowered on the
column for convenience in packaging. To raise the head,
proceed as follows:
1.
Place a block of wood, about 7" long. between the drill
press head and the table, as close to the column as possible.
2.
Make sure the collar at the bottom of the raising
mechanism rack is tight on the column and unlock the table
clamp. Then loosen the two bolts, located on the right hand
side of the head, that lock the head to the column.
3.
Turn the raising mechanism hand crank clockwise to raise
the table and head simultaneously.
4.
When the table approaches the top of the raising
mechanism, lock the table and head to the column. Then
loosen the raising mechanism collar and turn the raising
mechanism hand crank counter-clockwise. This will slide the
rack of the raising mechanism further up the column.
5.
Repeat STEPS 2, 3 and 4 until the top of the head is at
the desired height. Be sure not to raise the top of the head
casting beyond the top end of the column.
6.
With the head and table still loose, visually line up the
spindle with center of the base and lock the head to the
column.
7.
Position the table and raising mechanism to the desired
position on the column and lock them in place.
The table and all other machined or unpainted surfaces of the
drill press are protected with a coating of rust preventive. This
coating may be removed with a soft cloth moistened with
kerosene (do not use acetone, gasoline or lacquer thinner for
this purpose.) After cleaning, cover all unpainted surfaces with
a light film of good machine oil.
MOTORS AND SPEEDS
Rockwell 3/4 hp or 1 hp 81/2" frame motors may be used on 17"
Drill Presses. However, 3/4 hp motors should not be used for
any power feed or variable speed machines when they are
intended for full capacities.
With a 1140 rpm motor, spindle speeds between 230 and 2830
rpm can be obtained.
With a 1725 rpm motor, spindle speeds between 350 to 4250
rpm can be obtained
When selecting a motor of any other make, be certain that it
has the above specifications and is a NEMA 182 frame motor.
Also be sure it is protected against loss of lubricant when
operated in a vertical position.
When assembled to the drill press, the motor should turn in a
clockwise direction as viewed from the top.
ADJUSTING SPINDLE
RETURN SPRING
For the purpose of automatically returning the spindle upward
after a hole has been drilled, a spring is provided enclosed in
the case (A) Fig. 1, and is located on the left side of the drill
press head. This spring has been properly adjusted at the
factory and this adjustment should not be disturbed unless
absolutely necessary.
If it should become necessary to adjust it, proceed as follows:
1.
Back off the two nuts (B) Fig. 1. NOTE: Do not remove
the inside nut from the shaft. The nuts (B) should be backed
off just far enough so that the spring housing (A) can be
disengaged from the roll pin in the head casting.
2.
With a firm hold on the spring housing (A) Fig. 1,
disengage it from the pin in the drill press head, by pulling the
housing straight out, and turn the housing counterclockwise to
increase or clockwise to decrease tension. CAUTION: BE
CAREFUL NOT TO BOTTOM THE RETURN SPRING WHILE
TURNING THE HOUSING COUNTERCLOCKWISE. THERE
SHOULD BE ENOUGH SLACK LEFT IN THE SPRING TO
PERMIT LOWERING THE SPINDLE THE FULL AMOUNT OF
TRAVEL. Be sure the pin in the drill press head is engaged
with the spring housing before releasing grip.
3.
Retighten the two nuts (B) Fig. 1. NOTE: Do not over-
tighten the inside nut against the spring housing (A) as this
may cause binding of the pinion shaft.
4.
The tension of the spring can be tested by turning pilot
wheel counterclockwise. Be sure quill is not locked while
testing.
NOTE: The spindle return spring will lift approximately 40
pounds. When tapping heads, multiple spindles, or other
heavy tooling is mounted on the quill or spindle of your
machine, the use of our Cat. No. 17-838 Booster Spindle
Return Spring Kit, along with the return spring supplied
with your drill press, will enable the spindle to lift
approximately 80 pounds.
Fig. 1
3
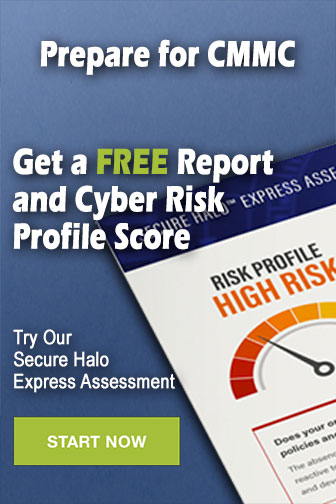