CALIBRATING SPINDLE SPEEDS
1.
Turn on the motor and set the pointer (B) Fig. 15, to
the lowest speed. (Either 350 or 230 rpm.)
2.
Loosen the hex lock nut and then adjust screw (C)
Fig. 15, to provide a positive stop for the pointer at the
lowest speed. The best way is to turn the screw
clockwise (up) until the pointer cannot be turned to the
lowest speed, and then turn the screw counter clockwise
(down) a little at a time until the pointer is stopped
positively, just as it comes to the lowest speed. Tighten
the hex lock nut.
3.
Increase the speed until the pointer is set at the
highest speed. (4250 or 2830 rpm.) Loosen the hex lock
nut and adjust the screw (D) Fig. 15, until the spindle
pulley is stopped from opening any additional amount,
just as the pointer shows 4250 (or 2830) rpm. The
pointer will go on past the mark, but there will be no
actual change in spindle speeds or pulley opening
beyond the movement allowed by stop screw (D), Fig.
15. Tighten the hex nut.
4.
With the pointer at the highest speed, the outside
circumference of the belt should now protrude about
1/32" beyond the outside circumference of the motor
pulley. If the belt does not protrude enough, move the
motor plate in toward the head, until the clearance is a
little bit less than 7/8", as mentioned in paragraph 4
under INSTALLATING MOTOR AND BELT. If the belt
protrudes too much, the clearance between head and
motor plate should be increased. (Be sure to keep the
motor shaft parallel with the spindle of the drill press.)
5.
When greater accuracy is required, a tachometer
should be used. Before following steps 1 through 4
above, proceed as follows.
6.
Turn on the motor and turn the pilot wheel (A) Fig.
15 counter clockwise, until the tachometer shows a
speed of 350 or 230 rpm, depending on whether the
motor runs at 1725 or 1140 rpm. Then, without
changing speeds, adjust the pilot wheel so that the
pointer shows exactly 350 (or 230) rpm. This adjustment
is made as follows.
7.
Unscrew and remove the two spokes (A) of the pilot
wheel shown in Fig. 15. Then loosen the two set
screws found in the holes thus exposed in the hub of the
pilot wheel and rotate the hub so that pointer (B)
indicates the lowest speed on the dial. Tighten the two
set screws and replace the two spokes.
8.
Follow steps 2, 3 and 4. After completing step 4,
check the top speed with the tachometer. If necessary,
move the motor plate in to increase the spindle speed as
shown on the tachometer or out to decrease it.
9.
If the motor plate is moved in or out in step 8, above,
the lowest speed will be affected, percentage wise, the
same as the highest speed. But the change in fpm will
be very slight at the lowest speed setting. No further
adjustment of the lowest speed is recommended.
Fig. 15
SPECIAL NOTE
The tension on the belt is governed by the specially
engineered spring of the motor pulley. No adjustment is
possible to change the belt tension. If the speeds are
properly calibrated and the pulleys properly lined up, the
correct belt tension will be maintained automatically
regardless of normal wear on the belt and the pulleys.
This feature provides long belt life by avoiding the
slippage which is experienced due to insufficient tension
on belt drives which are not fully engineered. The
automatic belt tensioning feature also provides longer
bearing life in both drill press and motor, because
excessive belt tension is avoided.
After a long period of time pulley and belt wear and
stretching of the belt may cause a slight change in the
speed of the drill press. To compensate for this change
in speed, use a tachometer and move the motor toward
or away from the spindle pulley until the correct speed is
obtained.
9
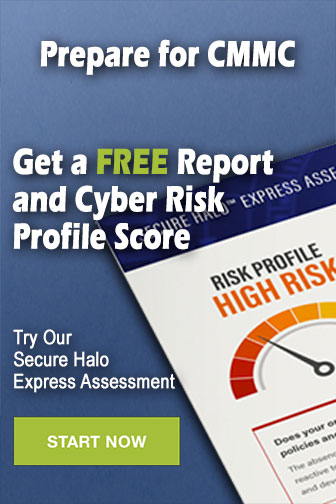