check thrust
13.
Replace drive link (8) into mesh
bearing operation
with coupling shaft (11 ) and -exert
a downward force on it with the
palm of one hand while pulling
down and rotating the coupling
shaft with the other hand; SEE
FIGURE 16. A damaged thrust
bearing (14) package would be
indicated by roughness "felt" or
heard during this procedure and
would require thrust bearing and
thrust washer (13) removal for
further inspection in subsequent
procedures. Remove drive link.
check coupling
14.
Check exposed portion of coupling
shaft for rust or
shaft (11) to be sure you have
corrosion
removed all signs of rust and
corrosion which might prevent its
withdrawal through the seal.
Crocus cloth or fine emery paper
may be used. SEE FIGURE 17.
remove & inspect
15.
Remove coupling shaft (11), by
coupling shaft
pushing on the output end of
shaft. Inspect coupling shaft
bearing and seal surfaces for
spalling, nicks, grooves, severe
wear or corrosion and discolora-
tion. SEE FIGURE 18. Inspect for
damaged or worn internal and ex-
ternal splines, drive pin slot, and
keyway. SEE FIGURE 19. Replace
coupling shaft if any of these con-
ditions exist.
NOTE
NOTE: Minor shaft wear in seal
(17) area is permissible. If wear
exceeds .020 inches (.51mm)
diametrically, replace coupling
shaft.
A slight "polish" is permissible in
the shaft bearing areas. Anything
more would require coupling shaft
replacement.
NOTE
NOTE: If commutator (9) was
discarded as worn or damaged in
Step 10, discard housing (15)
assembly as well. If this is the
case, the disassembly of the MAF
TorqmotorTM is now complete. If,
however, the commutator passed
inspection, continue the
disassembly procedures.
12
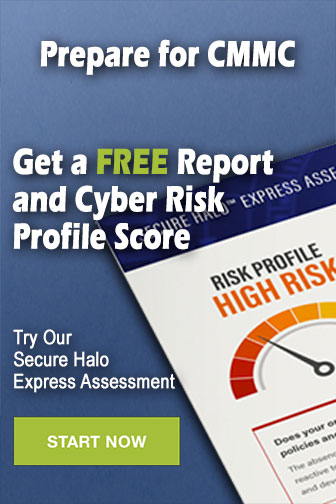